When you walk into SRC’s Pipe Flow Technology Centre™, you can’t help but feel that something really important is happening within its walls. At Pipe Flow, SRC’s experts and technologists work on solutions to real-world industry challenges—what they develop gets applied to field situations for testing and, if all goes well, implementation.
The second thing you notice are all the pipe loops of varying sizes that run across different areas of the facility. Inside the loops is where the magic happens, where experts study the transport of slurry through a pipeline, also known as slurry fluid mechanics.
During mining, ore (a solid) is mixed with water (a liquid), which creates a slurry. This is common in mining operations where at some point in the extraction process water and chemicals are mixed with ore to help extract the minerals of interest. Frequently during mineral processing, fluids need to be transferred from one area of the plant to another, or to the tailings pond once extraction is complete.
SRC’s Pipe Flow Technology Centre™ offers mining and other resource developers a unique opportunity to study slurries and test industrial samples and processes in a controlled environment that mimics the client’s actual operating conditions.
The data generated from this testwork is then used by the Pipe Flow’s experts to better understand, and improve, the client’s operations.
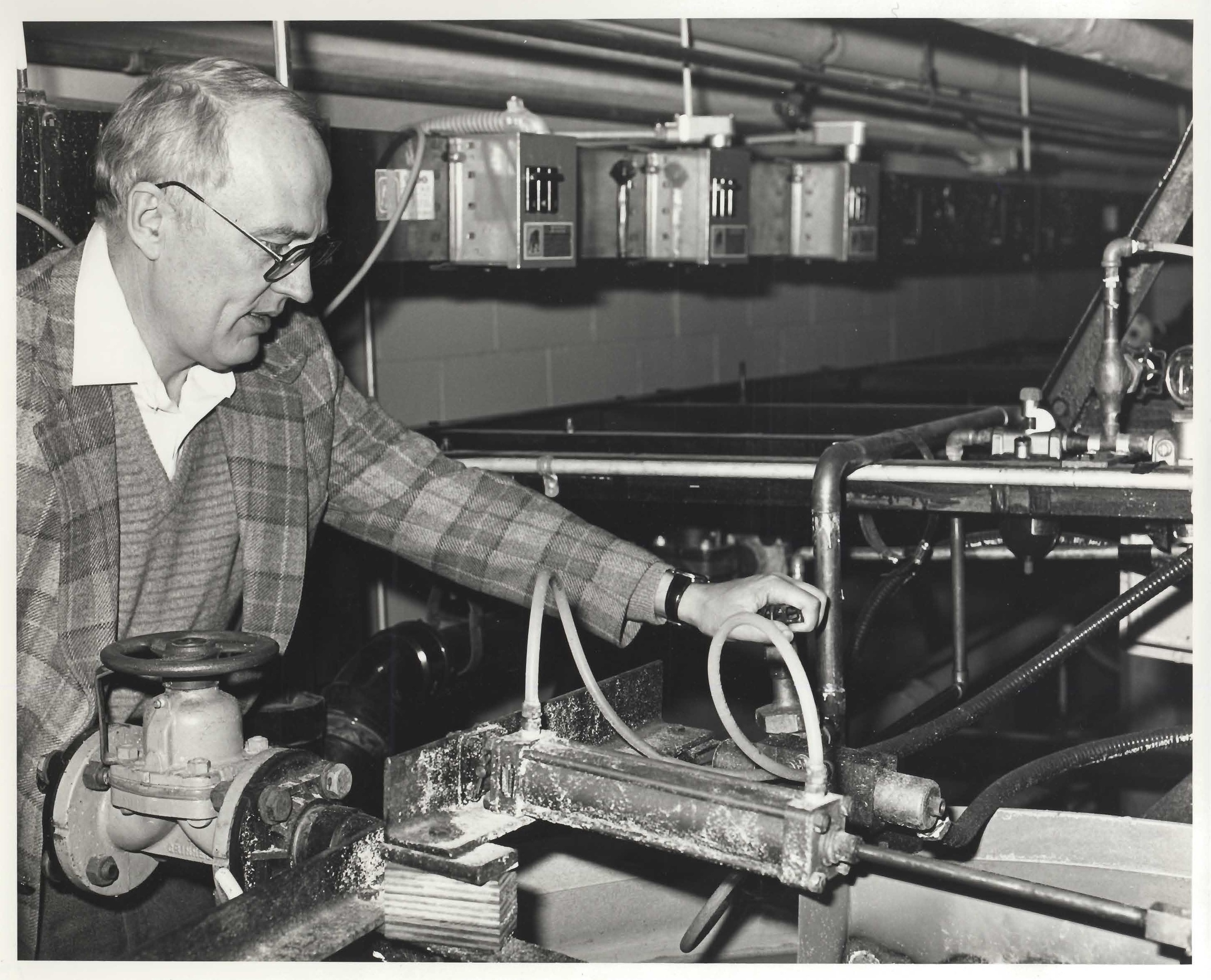
A Pipe Dream
Pipe Flow is celebrating its 60th anniversary in 2020. Looking back over 60 years, there are key people who were instrumental in developing the facility’s foundation and culture of learning, starting in the 1960s with Dr. Cliff Shook.
At that time, Dr. Shook was a professor in the College of Engineering at the University of Saskatchewan. He saw the potential of SRC’s technologists and with SRC’s Engineering Division, led by Bill Husband, initiated a slurry pipeline research program, which eventually became the Pipe Flow Technology Centre™.
An accumulated understanding of slurry flows laid the foundation for the development of the first SRC Pipe Flow Model, a primarily mechanistic model that describes the pipeline flow of settling slurries. Built on historical research from hundreds of slurry pipeline research and development programs, the SRC Pipe Flow Model has continued to progress from its origins in 1980, as the understanding of slurry flows continues to improve.
In 2013, SRC developed a Multi-Species Pipe Flow Model, which was primarily the work of Dr. Randy Gillies, a crowning achievement to his 38-year career with SRC. Even though he retired several years ago, Dr. Gillies still contributes to client work and model improvements as an SRC Researcher Emeritus.
Both models are industry standards for slurry transport design, particularly for the oil sands industry in Canada. SRC shares these models with industry through courses, including the Slurry Pipeline Systems Course, taught jointly with Paterson and Cooke. The foundational slurry course has been taught to over 700 industry professionals from around the world, while the multi-species course (launched in 2015) has reached over 100 participants to date.
Dr. Shook and Dr. Gillies led the development of SRC’s training approach to distributing the models.
A Collaborative, Integrated Team
This culture of learning and sharing has been preserved throughout the years as Pipe Flow’s team has evolved to meet industry needs.
It takes team effort to come up with the right solutions for clients. The team has risen to the challenge many times, whether it’s something new or something different that hasn’t been done before.
Collaboration also plays a big role, both internally and externally, to solve industry challenges; often, with industry themselves.
Pipe Flow has been involved in some bigger, multi-client projects that involves bringing together experts from a variety of industries and specialties, including Dr. Sean Sanders at the University of Alberta and Rob Cooke from Paterson and Cooke.
Weathering the Storms
2020 was a challenging year all around but hit the oil and gas industry particularly hard. Things are getting busier again at the facility with clients, who had scrimped and saved during the worst part of the pandemic, now keen to get back in the lab.
Some of the projects the facility is working on now aren’t dramatically different than they would’ve been 10 or 20 years ago, but one thing that has changed is the instrumentation the facility has to work with.
One example is their 2-D Gamma Ray Tomography (GRT) unit, which helps SRC’s experts better understand slurry flows. With any new technology comes a learning curve, too. Pipe Flow’s experts had to develop the techniques and methods to analyze the GRT’s data.
Another example is the opening of the Shook-Gillies HPHT Facility in 2015, which is capable of handling volatile materials and is equipped with a high-pressure, high-temperature flow loop.
Sometimes a new technology comes out of developing expertise, such as the work the Pipe Flow is doing on instrumentation development for clay analysis. The team was successful in obtaining funding from NRCAN’s Clean Growth Program for a project, led by SRC with Suncor Energy Inc. and the Northern Alberta Institute of Technology as partners.
The project involves developing a technology to provide near real-time measurements of the active clay content in oil sands and mine tailings. This technology is important to enhance tailings treatment technologies, which are something SRC has been active in trialing with industry over the past decade.
Clearly, none of this expertise is developed over night. It’s been a culmination of studying slurry fluid mechanics for over 60 years.
The Future of Pipe Flow
What does the next 60 years look like at the Pipe Flow Technology Centre™?
With mounting pressure from the public and regulators, you can imagine the environment is top of mind for industry—it’s not a trend, but a new way of thinking. Projects with an environmental focus have accounted for a significant portion of Pipe Flow’s work for several years, but particularly over the last decade.
While emission reductions aren’t traditionally in Pipe Flow’s scope of work, Pipe Flow can leverage equipment and experience from working with oil sands and mining clients, as well as draw on other expertise from within SRC.
It goes back to the notion of problem solving, which requires having the right people and the right tools —something SRC’s Pipe Flow Technology Centre™ has developed over the past 60 years.