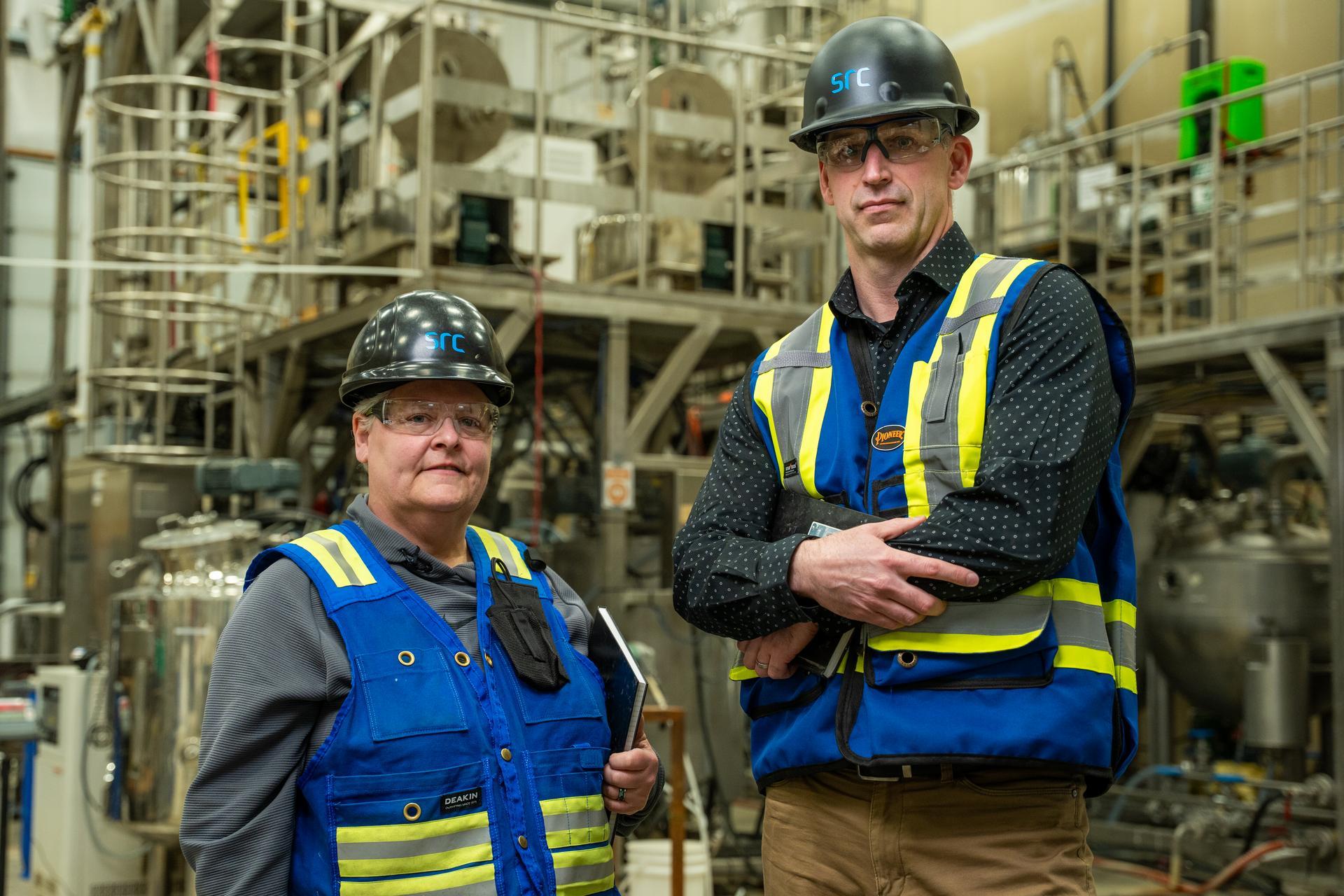
From environmental remediation in the Athabasca Basin to renewable energy storage systems in southern Saskatchewan, SRC is committed to tackling every project — large or small — with the health and safety of its employees top of mind.
Beginning in 1959, SRC’s safety program has evolved over the last several decades and continues to be shaped by the innovative and leading-edge work SRC undertakes. What does safety look like at SRC now compared to the past and how does an organization keep employees engaged along the way? We sat down with a couple members of the Safety Services team at SRC to get their insight into the important role of safety in the workplace.
Safety is everyone’s responsibility
“Safety is definitely a shared responsibility, with everyone having a role to play,” said Kenelm Grismer, Director of Health, Safety and Risk at SRC. “As an employer, SRC has the responsibility to establish and maintain an effective safety management system to enable people to work safely.”
The management system is driven by safety leadership and commitment at all levels of the organization and includes upholding SRC’s organizational philosophy that safety is an overriding priority.
With SRC providing the foundation for this safety culture, employees are empowered in their work environment to perform their work safely, making sure that they are confident they understand the hazards and are equipped to do the job safely before they proceed. To ensure safety across the Council, it’s important that employees know and practice their rights, including the right to refuse any unsafe work.
“We want employees to be curious about safety, to ask questions and to challenge the way that we do our work to ensure it’s being done in the safest way practical,” said Grismer.
Managers and supervisors have the responsibility to ensure that employees receive the appropriate training and tools for their roles, as well as to ensure that employees are following the established rules and procedures. They lead by example to reinforce SRC’s commitment to safety.
SRC’s occupational health and safety committees provide a forum for the employer and employees to work together to continually improve safety.
“Collectively, these various roles create layers of defence to keep us all safe,” said Grismer. “Each of these roles are vital to developing and maintaining a strong safety culture across SRC.”
Varied service lines create unique safety requirements
From lab benches to field work to desk duties, every team at SRC encounters different risks and hazards, but Grismer says that doesn’t change the Council’s philosophy.
“Across SRC, safety is an overriding priority. All groups operate under the same overarching safety management framework, but how the tools are applied may change between groups,” said Grismer.
SRC has several laboratories that process samples, providing data and insight to clients around the world. In these spaces, employees often engage in routine work, drawing more heavily on well-established standard operating procedures and safe work practices.
Other employees, like those in the field doing air quality testing, may encounter levels of uncertainty with varying day-to-day tasks. These employees need to conduct regular field level risk assessments and be comfortable identifying and mitigating hazards in changing conditions. Grismer says this is where safety training and experience is crucial.
As SRC evolves, new projects come together and new business units are established. Often these growing and specialized teams need to develop new safety protocols for their work.
For instance, the developmental nature of the work that SRC’s Research and Development team does in its Rare Earth Element Division comes with a certain amount of risk and uncertainty when doing something for the first time, which is why planning, training and having the right tools for the job is critical.
“They’ve worked very hard to assess the hazards, develop standard operating procedures and safety protocols to mitigate the risk and spend a significant amount of time and effort in training the team to conduct the work safely,” said Jackie Foord, SRC’s Occupational Health and Safety Lead. “They are continually reassessing the risks and refining the way they do the work to improve safety. The planning and development they’re doing now will benefit the operation in the long term.”
SRC’s safety management framework, driven by the organizational commitment to safety, positions SRC well to meet the various safety challenges that are encountered working across a number of diverse service lines.
Safety evolves alongside SRC
In the last five years, SRC has expanded into growing sectors like critical minerals. These new projects have not only required specialized knowledge and expertise but also new equipment and facilities, such as SRC’s under construction Rare Earth Processing Facility and its Minerals Liberation Sorting Centre.
“These types of projects have definitely been a catalyst to advance our safety program on a number of fronts,” said Grismer.
New skillsets and resources brought on to carry out these projects have enabled SRC to look at work environments from a variety of perspectives and teams work together to find solutions to challenges.
“Working with tradespeople who have come from larger organizations, such as mining operations,” said Foord, “brings a wealth of knowledge to the organization regarding safety.”
These projects carry with them unique safety needs. Foord says that the extensive efforts invested in activities such as hazard assessment, planning and training has been and continues to be critical to the success of these projects and to ensuring everyone on site goes home safe at the end of the day.
New safety innovations keep employees at the heart of safety
SRC’s Safety team continues to innovate to meet the Council’s needs for new and existing projects and facilities in 2025 and beyond.
As SRC’s industrial process operations expand, so do its safety requirements. Tools like automation, robotics and artificial intelligence will help improve safety by mitigating hazards, as well as provide opportunities for enhancing and streamlining data analysis and reporting.
And while new tools, techniques and approaches can help improve safety, people and their commitment to safety remain at the centre of SRC’s safety philosophy.
“Innovation has been critical to working safely across SRC. As an organization, we are fortunate to have access to a wide range of expertise and skillsets, from engineers and scientists to instrument techs and electricians,” said Grismer.
Learning from employees’ experiences on site, in the field and at the lab bench helps SRC improve its protocols and approaches to ensure they are robust enough to tackle any safety challenges.
“We are continuously applying these resources to advance safety, both for our clients as well as our own operations. There are countless examples of situations where a team identified a hazard and developed an innovative approach that enabled them to do the job more safely,” said Grismer.
SRC’s goal is ultimately to eliminate workplace injuries. To achieve that goal, the focus is on continuing to ensure that all employees at SRC feel they are accountable for safety and are empowered to ensure work is done safely.