This is a contributed blog post written by former SRC employee, Andy Goodson.
If you’ve shopped for a new washing machine or dryer recently, you may have been surprised to find that some new models include WiFi connectivity built in. This feature gives you the ability to monitor loads, or even change the cycle time from your phone. It is an example of the Internet of Things (IoT) – connecting ordinarily mundane devices to the Internet to give you greater knowledge and control of their functions.
But IoT goes far beyond household appliances. The core technology of IoT has been around for a while and its use by industry is becoming increasingly common. It is one facet of Industry 4.0, what some are calling the Fourth Industrial Revolution, the trend toward device interconnectivity and automation in manufacturing.1
As the components required to build an IoT system become smaller, cheaper and more robust, the increased practicality of IoT allows industry to leverage an unprecedented amount of data.
How does the Internet of Things work?
The Internet is a network of devices exchanging information. Just like people must understand each others’ languages to have a conversation, devices must understand how to communicate with other devices as well. A common set of rules is needed.
The Internet solves this challenge using protocols — essentially an agreed upon set of rules for how devices talk to each other. This allows devices from anywhere in the world to transfer and receive data without the message becoming lost, damaged in the process or, in other words, misunderstood. It is often compared to a mail system, where each letter or parcel has a send and return address and the contents must be of a certain size, type or format.
Like most public infrastructure, the Internet can be used freely by all — non-living things included. The IoT uses this existing network for ordinary devices to communicate, without human interaction.
When you add small, easily affordable sensors and transmitters to the mix, the amount of data collected can be mountainous. Being able to store and process this information at remote data centers over the Internet – a larger concept known as cloud computing – is the crux of the IoT and what makes it practical for more advanced applications today.
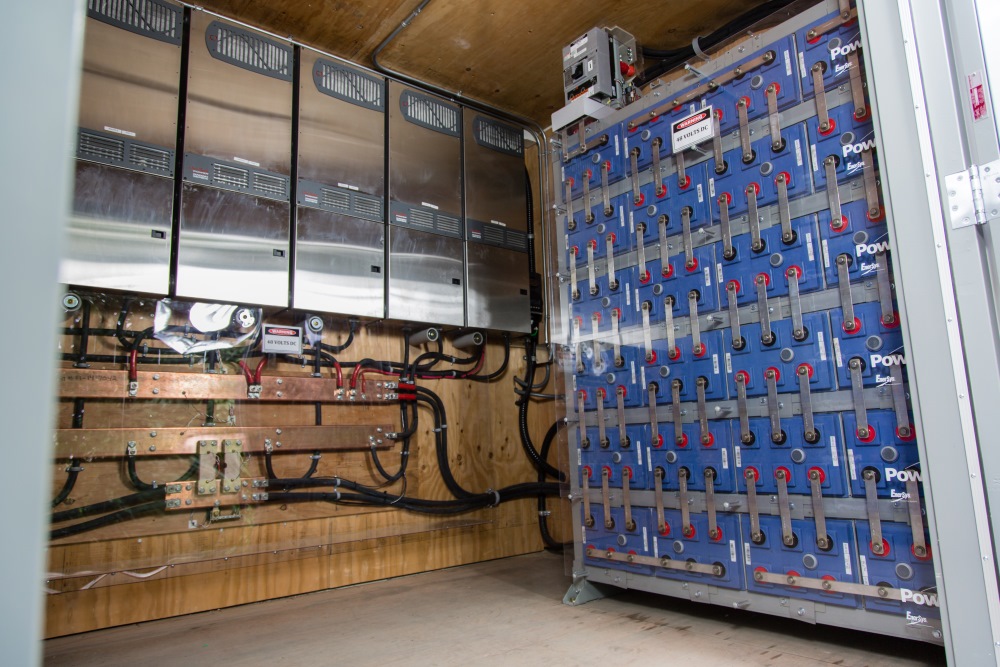
Enter the Industrial Internet of Things
The Industrial Internet of Things (IIoT) is simply the IoT in an industrial setting. But unlike consumer-grade appliances like refrigerators and toasters, industrial machinery and scientific instrumentation require a few more checks and balances.
The value of IIoT is that it allows companies to take advantage of existing infrastructure to automate processes requiring data collection; there is no need to build internal networks or data centers from scratch. With low-cost, high-quality sensors becoming more accessible, the IoT may soon become ubiquitous in industrial processes.
Nathan Peter, Digital Systems Lead for SRC’s Development Engineering team, says, “Industry has used computing and data communication technologies for many years...these systems were typically built with infrastructure that was independent of public Internet networks. IIoT is accomplishing the same remote monitoring and control objectives, but with Internet-connected devices.”
But there are still challenges to face before IIoT systems are commonplace. Security and data quality are the most obvious hurdles, which require a level of expertise to assess needs, plan equipment and install systems safely and efficiently. If critical processes are involved – which is often the case in industrial workplaces – concerns about privacy, reliability and remote access are extremely important.
The challenges of end-to-end design for IIoT systems is something SRC’s Development Engineering team work to resolve. Nathan Peter identified the three most important considerations when developing an IIoT system:
- Network security and reliability – protecting data in transit through encryption and working within the constraints of network communications, including limitations around bandwidth, latency and continuity (e.g., how communications are affected by network outages.)
- Data security – managing big data and controlling access to vast amounts of sensitive information, including financial, technical and intellectual property.
- Remote access to field devices – making sure only authorized personnel have access to devices that have real-world functions, such as cameras, actuators and output switches. This includes being aware of back-door vulnerabilities embedded in the hardware.
What opportunities does the Industrial Internet of Things create?
An IIoT system can be any number of Internet-connected sensors embedded in a process that help experts diagnose problems and make decisions from anywhere in the world. It can be as simple as a network of sensors tracking pressure cycles along a pipeline, or it can be part of a larger automation process.
Mundane or repetitive tasks that once required personnel can be programmed, improving data reliability and removing humans from potentially harmful environments.2 And as more affordable sensors make the technology accessible, companies are pressured to create new, innovative ways to operate more safely, efficiently and at a lower cost with competition driving the process.
Here are a few key areas where the IIoT may excel in industrial applications:
- Transparency – Access to real-time data, which can be instantly logged and reported, may improve how companies meet their regulatory requirements. The data is instantaneous and may be more reliable as it removes the chance of human error. It also benefits companies by saving time that would otherwise be spent conducting in-person inspections and correspondence.
- Optimization – Expenses can be reduced as ‘intelligent’ systems are theoretically able to find where inefficiencies are cropping up and then manage them. This could be like automating specific functions, so they occur during times of lower operating cost. Data can also be used to monitor the condition or wear-and-tear of mechanical parts, allowing for preventative measures to take place and reduce downtime.
- Safety – A continuous flow of data means problems that would otherwise be missed between inspections can be detected immediately. This has enormous implications, not only for industry, but for the public too, as applications in environmental monitoring may build more robust advance warning systems.
- Remote operability – In a decentralized world, the ability to perform duties from remote locations is a major advantage. This allows technologists and experts to diagnose complex problems, regardless of their geographic location.
The main feature of the IIoT is the enormous amount of data it collects, making the list of potential uses almost boundless. The question becomes one about innovation and finding new ways to harness a wealth of data for practical purposes.
References
- Hermann, Pentek, Otto, 2016: Design Principles for Industrie 4.0 Scenarios
- Linda Rosencrance, Sharon Shea and Laura Aberle: A comprehensive guide to enterprise IoT project success, What is the Industrial Internet of Things? (IIoT)